Expansion of Expandable Polystyrene (EPS)
Expansion Basics • Heat Is Applied • Beads Expand • Beads Cool • Beads Age
Expansion – Behind the Scenes • Heat Is Applied • Blowing agent(s) vaporizes (28oC iso-pentane, 35oC normal-pentane, 49oC cyclo-pentane) • Blowing agent(s) permeate through the polymer (n-pentane<i-pentane<c-pentane)
Expansion – Behind the Scenes • Beads Expand • Polymer/blowing agent matrix reaches it’s glass transition temperature (Tg) (about 85oC, varies according to Mw & BA type) • Polymer chains become fluid • Internal pressure created by blowing agent vaporization push apart [unfold] polymer chains, creating cells
Expansion – Behind the Scenes
Expansion – Behind the Scenes • Beads Expand (cont.) • Air & steam permeate into the beads • As expansion continues, cell walls become thin and subjection to high heat can cause them to break and rupture
Expansion – Behind the Scenes • Beads Expand (cont.) • Throughout expansion, blowing agent(s) continue(s) to permeate out of the bead at an increasing rate [depending on temperature and thickness of cell walls] (When permeation rate =/> vaporization rate, expansion ceases)
Blowing agents begin to vaporize Polymer/blowing agent matrix reaches its Tg Cell walls begin to rupture Expansion begins after reaching Tg and proceeds rapidly Loss of blowing agent becomes more rapid as temperature increases
Primary Expansion Controls • Temperature • Time
Temperature Affects • Greater the temperature • Softer the polymer • Increased expansion rate • May result in uneven expansion due to inconsistent • pentane content • bead size • cell structure • raw material “carry over” [extreme cases] • Increased permeation rate of blowing agent
Expansion verses Temperature • <100oC • Expansion can be sluggish due to stiff polymer • >120oC • Polymer is too soft, blowing agent loss is too rapid • 110-120oC • Most efficient use of blowing agent, but beads become sensitive to shrinkage and heat • 100-110oC • Best compromise
Steam Quality • Key to Expansion • Consistent utilities are crucial to achieve consistent densities with consistent volatile content
Secondary Expansion Controls • Volume of Expander • Molecular Weight • Blowing Agent • Bead Size
Expander Volume Affects the total heat available to each bead • Things that can change it • Drop/charge weight • Lumps in expander that don’t discharge • Build up on walls or stir blades
Molecular Weight • The lower the molecular weight, • Increased expandability • Increased heat sensitivity • Increased permeation rate of blowing agent • Increased shrinkage • Increased collapse • Structural strength
Blowing Agent • Amount • Higher percentages give greater expandability (to a point) • Too high a percentage causes rapid permeation thus shrinkage, collapse and heat sensitivity
Blowing Agent • Type • The longer the blowing agent stays in the bead, • Increased expandability • Reduced shrinkage rate • Increased prepuff life (from expansion to mold) • Relative retention n-pentane < i-pentane < c-pentane
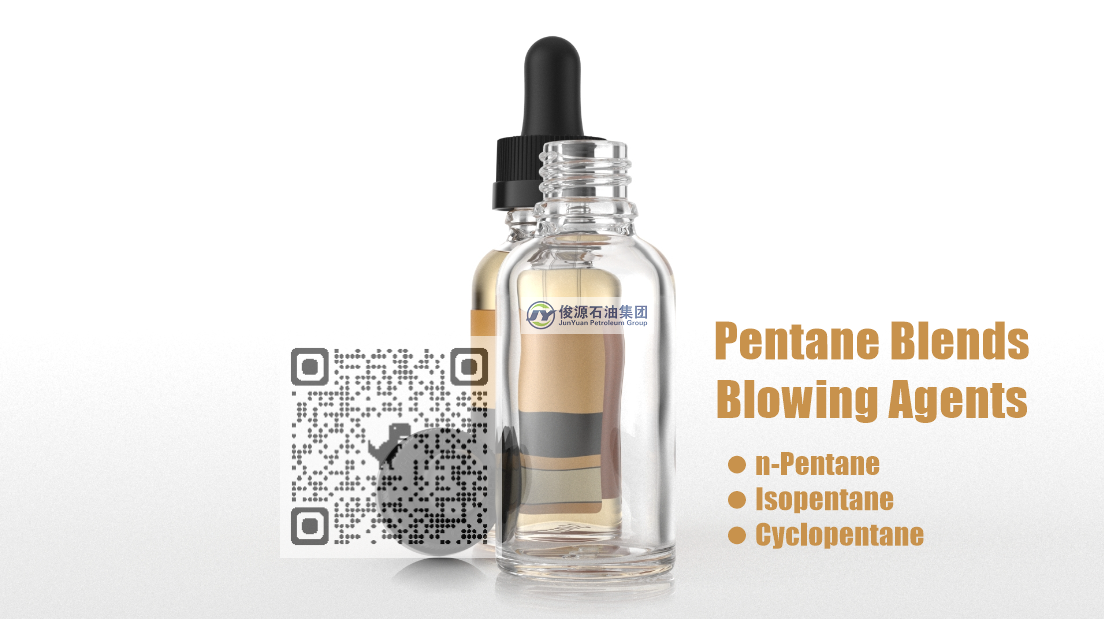
Blowing Agent • Degree of Distribution (has a direct affect on cell size) • Expandability • Heat sensitivity • Structural strength • R-Factor (insulation properties) • Permeation rate
Poor Distribution of Blowing Agent Blowing Agent Good Distribution of Blowing Agent
Bead Size • The larger the bead, the easier it is to achieve low densities • Less surface area for blowing agent to permeate out of
Expander Equipment • Continuous • Batch • Wet • Dry
Continuous Expanders • Description • Material is fed into the bottom of the expansion chamber where it is subjected to steam under agitation, material expands and as density decreases, material rises to the top and out the exit chute. • Rely on Time & Temperature
Continuous Expanders • Main Controls • Feed rate • Steam pressure (temperature) • Agitation rate • Outlet height • Fresh air introduction (temperature)
Batch Expanders • Description • A pre-weighed quantity of material is dropped (or charged) into the expansion chamber where either the expander walls are jacketed with steam (dry) &/or steam is injected into the chamber (wet). An agitator keeps material moving. Vacuum, purge or water inject may be used to stop the expansion. • Rely on time, temperature &/or volume
Batch Expanders • Main Controls • Steam pressure (temperature) • Volume or height • Time • Charge weight • Vacuum or purge time • Water inject
Density Check • Consistency is the Key • Procedure • Prepuff is overfilled into a known volume (pre-tared) container. The container is vibrated or tapped (vibration is more consistent). A straight edge is used to strike the top level with the canister. The canister is reweighed and the density calculated.
Expansion – Behind the Scenes • Beads Age, a.k.a. Maturing or Stabilizing • Internal moisture [from condensed steam] permeates out of the bead • Air permeates into the bead until internal and external pressures equal • Blowing agent(s) continue(s) to permeate out of the bead (n-pentane>i-pentane>c-pentane)
Why Age Prepuff? • Foam becomes more resilient after it’s stabilized • Internal vacuum makes beads susceptible to deformation • Reduces blowing agent levels • Too high a blowing agent level leads to excessive cool times and heat sensitivity during molding • Dry prepuff • Improves ease of transportation
Volatile Content on Aging
Aging • Key • A consistent environment is important to provide prepuff to mold with a consistent volatile content
Aging Time Controls • Environment • Air flow Time • Temperature Time • Density Time • Bead Size Time • Blowing Agent Type(boiling point & molecular complexity) Time • Polymer Mw Time
Expansion – Troubleshooting • High Density • Insufficient steam pressure/temperature • check traps, valves, accumulator pressure • steam flow restricted Note: by monitoring both steam pressure and steam temperature, you’ll know your steam quality. • Insufficient steam times • Too high a throughput through expander (continuous) gives raw material carry-over • Wet material
Expansion – Troubleshooting • High Density (continued) • Collapsed or over expanded prepuff • Low blowing agent content in raw EPS • Additive problem (block and shape EPS grades) • Increased drop weight • Electric eye level too low
Expansion – Troubleshooting • Low Density • High steam pressure/temperature • Longer steam times • Reduced drop/charge weight • Wet material • Over dried material • High blowing agent content • Surface additives (block & shape grade EPS) • Electric eye level too high
Expansion – Troubleshooting • Density Fluctuations • Inconsistent steam pressure/temperature • Inconsistent steam time • Erratic drop/charge weights • Inconsistent measuring techniques • Inconsistent blowing agent content • High static (affects electric eye)
Expansion – Troubleshooting • Density Fluctuations (continued) • Purge valve sticking • Vacuum problems • Inconsistent water inject volume • Poor additive distribution (block & shape grade EPS)
Expansion – Troubleshooting • Wet Prepuff • Common on expander start up • Wet steam • Purge valve or vacuum not working • Poor air flow through fluid bed dryer • Too much material in the fluid bed dryer
Expansion – Troubleshooting • Bead Collapse • Over-expanded • Excessive steam pressure/temperature • Excessive steam time • Too high an expansion rate • Thermal shock after expansion • Blades too close to walls or bottom of expansion chamber • Wrong additive package (block and shape grade EPS)
Expansion – Troubleshooting • Lumping • Too much moisture (condensate) • Inadequate stirring • Excessive steam pressure/temperature • Anti-lumping agent level too low • Hot spots in expander • Excessive steam time
Expansion – Troubleshooting • Irregular Prepuff (size/appearance) • Poor or irregular steam flow • Hot spots in expander • Insufficient time in expander • Contamination of prepuff in raw EPS (double pass) • Irregular raw EPS
Pentane
Pentane is a colorless, flammable liquid (the first liquid member of the alkanes) that is lighter than water. It has a pleasant odor that can be detected at 900 ppm, and a moderate odor intensity is observed at 5000 ppm. It occurs as two other isomers, including isopentane [(CH3)2CHCH2CH3] and neopentane [C(CH3)4]. Isopentane (2-methylbutane) apparently has physical and physiological characteristics similar to straight-chain pentane. Neopentane (2,2-dimethylpropane) is similar to butane in physical and physiological characteristics. In air, one part per million of C5 pentane is equivalent to 3 mg m−3.
Modifying Processing Characteristics: Blowing Agents
It is expected that the trend towards use of carbon dioxide will continue but, where it is not possible to achieve the necessary properties, flammable organic compounds will be used. Expensive, partially fluorinated HFCs with their relatively high GWP will only be used where non-flammability is essential. Chlorine-containing compounds, however, must be replaced completely.
Pentane presents itself as a possible solution to finding an efficient blowing agent which also meets environmental regulations, and years of experience in using it have shown that processing can be safe, as long as safety devices are fully implemented. Bayer’s PU machinery subsidiary, Hennecke GmbH, has developed a state-of-the-art system that monitors all critical control points along the processing chain, to ensure safe production. Among the features are:
•
completely encapsulated machinery and units (including in-line blenders, work tank, and high-pressure reaction casting machine), also aerated and fitted with exhaust devices, pentane gas sensors, and other safety devices;
•
a metering and blending supervisory system (Pentament), also permanently vented to prevent gas build up;
•
an electronic security system controlling all safety features, which can shut down operations, if necessary;
•
pentane gas warning sensors monitoring all critical components; and
•
an independent decentralized control system, alerted to all trouble indicators from primary and secondary sensors and monitors.
The modifications were designed to add safety checks to all critical points, first pinpointing all potential hazards (such as ignition sources, leakage points, and static charging) and then developing integrated safeguards.
Bayer and Apache Products have discovered that, by extrusion mixing of high levels of fillers and/or diluents in a PU formulation, loadings of 10–50% filler by weight can be achieved while maintaining or improving key physical properties. The technology makes it possible to handle high-viscosity dispersions effectively, which may reduce production costs of rigid boardstock. Use of solid fillers, solid combustion modifiers, and hollow fillers was studied, suggesting that the higher cost of hollow fillers can be offset by density reduction in the foam board and increase in compressive strength.
Use of this more environmentally friendly alternative may be facilitated for manufacturers of domestic appliances following the introduction of new safety features in the CycloFlex and LinFlex systems for refrigerator cabinet production. Hennecke Machinery has developed a comprehensive safety system for pentane-based foam production, meeting many of the reservations of US manufacturers of PU board.
The principle of Pentane Blowing Agent Use
Pentane blowing agent use the principle of foaming agent and foaming agent differentiation physical foaming agent. Chemical foaming agent is break down to form gas at high temperature decomposition ( N2, CO2, NH3, etc. ) Organic and inorganic substances. This is usually a exothermic decomposition process and irreversible. Physical foaming agent can be liquid, also can be in normal circumstances have vaporized material. The physical foaming agent including aliphatic, hydrocarbons ( Pentane, hexane, decane, etc. ) 。 Chlorine hydrocarbon ( A the methane of cl, methylene chloride, etc. ) 。 Chlorine – Fluorocarbon compounds ( Cross-linked with methane, a fluorine dichlorodifluoromethane, etc. ) CO2, N2, rare gas and air. Regular physical foaming is refers to the the physical foaming agent and resin matrix mixing by changing the conditions in the process of operation; According to the principle of thermodynamic instability that changes the physical foaming agent.Then the process of generating bubbles.

THERMOSETTING FOAMS
Non–fluorinated blowing agents.
n–Pentane has been used in European countries, e.g., Germany, as a blowing agent for rigid urethane foams. According to Heiling and co–workers’ test results, it has been concluded that there were no indications of higher risks in the case of a real fire. Specifically, the fear concerning explosive–gas mixtures of pentane and air was not confirmed. Explosion–proof dispensing machines have been developed by some companies. Cyclopentane can also be used as a physical blowing agent.
Recently n–pentane–based blowing agents of a blend type have been patented. This patent claims the use of a blend of liquid hydrocarbon and chlorinated hydrocarbon, e.g., a blend of n–pentane and methylene chloride. This method is a convenient way to produce various rigid foams, e.g., polyurethane foams, polyisocyanurate foams, and polyoxazolidone foams. Methylene chloride and pentane have nearly equal boiling points and their blends act like a single solvent. The use of methylene chloride alone results in foam collapse, but a blend of the two solvents does not result in such collapse. A blend of 80/20–90/10 wt % of methylene chloride/pentane is substantially non–combustible, and can be used as the blowing agent for polyisocyanurate–based foams. For rigid polyurethane foams, a blend of about 50/50 wt % is suitable. These blends could solve the disadvantages of 100% water–blown rigid foams mentioned above.
What will be the next generation of blowing agents? Decaire et al. list the requirements for alternative blowing agents as follows: zero ozone depletion potential (ODP), non–flammable or moderately flammable, 50°C boiling point upper limit, and molecular weight below 180. In addition, the cost ($/mole) of a blowing agent is another important industrial factor.
The use of some azeotropic mixtures as blowing agents for rigid urethane foams have been proposed by Doerge. These blowing agents include CFC–11/methyl formate (238), and HCFC–141b/2–methyl butane. Ashida et al disclosed halogen–free azeotropes.
2–Chloropropane as blowing agent for rigid urethane foams has been developed by Recticel.
Mixed gas/liquid blowing agents for rigid urethane foams have also been proposed. The patent claims the use of hydrocarbons having boiling points (a) less than 10°C or (b) 20–30°C, or (c) an inert organic liquid having a boiling point of 35–125°C. Another mixed blowing agent for rigid urethane foams was proposed by a patent which claims the use of a mixture of cycloalkanes, e.g., cyclopentane and cyclohexane, and, if necessary, water The non–fluorinated blowing agents described above can also be applied to polyisocyanurate foams, polyoxazolidone foams, polyurea foams, etc.
Methylene chloride has been used as an auxiliary blowing agent for a long period of time. In some countries, however, due to possible occupational and environmental problems, increased restrictions have been placed on the use of methylene chloride. Therefore, other types of auxiliary blowing agents have been proposed.
Liquefied carbon dioxide is proposed as an auxiliary blowing agent for water–blown flexible urethane foams. Hydrocarbons having a boiling point of 38–100°C are proposed for use in self–skin foam production. Blends of hydrocarbons having a boiling point above −50°C and below 100°C have been proposed as auxiliary blowing agents for water–blown flexible foams.