Description
Refinery Applications
DTBPS (Di-tert-butyl Polysulfide) serves as a sulfiding agent, working in conjunction with a reducing agent like hydrogen. Its purpose is to convert metal oxide species into a crystalline metallic sulfide phase in situ for hydrotreating catalysts. By conducting the reaction within the process unit, operators maintain precise control and optimize catalyst activity while ensuring safety.
Safety and Handling
DTBPS (Di-tert-butyl Polysulfide) poses environmental hazards and qualifies as a marine pollutant. Its high viscosity presents challenges during cold weather handling. While it remains insoluble in water, it does dissolve in hexane and white spirits. DTBPS is compatible with both carbon and stainless steel, and for injection purposes, Teflon or Viton gaskets are advisable.
Comparison of Other Polysulfides
DTBPS (Di-tert-butyl Polysulfide) is a blend primarily composed of tetra and penta sulfides. Unlike a distilled material, it boasts the highest sulfur content among manufactured polysulfides. In addition to DTBPS, other available polysulfides include TNPS 537, TDPS 532, and TDPS 320. These products find application in the metalworking lubricant markets.
Performance Data
Technical Data Sheet of DTBPS (Di-tert-butyl Polysulfide)
Product Code: DTBPS
Chemical Components: Di-Tert-Butyl PolySulfide
Appearance: Light yellow to dark brown liquid
Features: Environmentally and safer. Non-flammable, with friendly odor. Low toxicity.
Molecular Formula: C8H18Sx
CAS: 68937-96-2
Items |
Specification |
Test Method |
Flash Point (opening cup),℃ |
≥100 |
GB/T 3536 |
Appearance |
Dark Brown or Tan Liquid |
Visual |
Odor |
Friendly odor |
– |
Solubility |
Insoluble in Water,
Miscible in Alcohol, Ether |
Visual |
Density(20℃), g/cm3 |
1.09-1.18 |
GB/T 4472 |
Sulfur, %(wt) |
53-60 |
GB/T 17040 |
Freezing Point |
≤-30 |
GB/T 510 |
Ash, %(wt) |
≤0.05 |
GB/T 508 |
Kinematic Viscosity(40℃), mm2/s |
To Be Reported |
GB/T 265 |
Initial Thermal Decomposition Temperature℃ |
125-150 |
GB/T22025 |
Advantages of DTBPS (Di-tert-butyl Polysulfide):
Performance data-DTBPS (Di-tert-butyl Polysulfide) vs DMDS
Typical Characteristics |
DMDS |
DTBPS |
Chemical Name |
Dimethyl Disulfide |
Di-tert-Butyl Polysulfide |
Sulfur Content(%,wt) |
68 |
55 |
Decomposition
Temperature℃ |
200 |
150 |
Flash Point℃ |
24 |
100 |
Appearance |
Light yellow liquid |
Dark brown liquid |
Odor |
Offensive odor |
Friendly odor |
Density(g/cm3) |
0.887 |
1.09-1.18 |
Freezing point℃ |
-85 |
-44 |
Water Solubility |
No |
No |
GHS |
Flammable |
None-flammable |
Application Guidelines
For in situ sulfiding of hydrotreating catalysts, the process typically involves several steps:
- Drying and Wetting: The catalysts are initially dried and then wetted with feed material at temperatures 300°F or below.
- DTBPS Injection: As the temperature approaches 400°F, DTBPS injection begins. The reactor is maintained within a range of 400–420°F until H2S breakthrough occurs.
- H2S Breakthrough: Breakthrough is indicated when the H2S level in the recycle gas exceeds 5000 ppm.
- Secondary Sulfiding Plateau: After breakthrough, the reactor temperature can be raised to the secondary sulfiding plateau, typically in the range of 620–670°F. This temperature is held for at least 4 hours to complete the sulfiding process.
- Secondary H2S Breakthrough: At this point, a secondary H2S breakthrough may occur, with H2S levels rapidly exceeding 20,000 ppm.
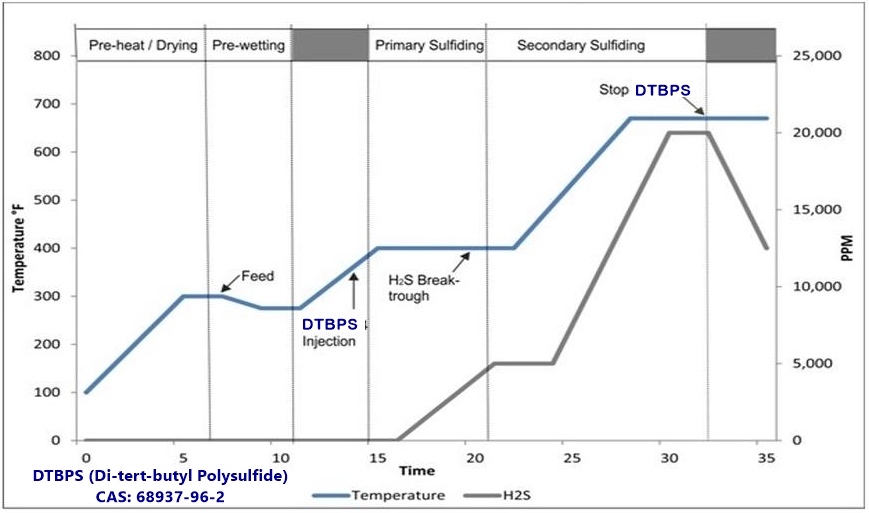
di-tert-butyl Polysulfide, DTBPS
Please note that this process ensures optimal catalyst activity and safety during hydrotreating.
Typical Feed Sulfiding Procedure
DTBPS (Di-tert-butyl Polysulfide) undergoes decomposition, resulting in the formation of elemental sulfur. When elemental sulfur combines with olefins, it can lead to the creation of a solid polymeric product. This risk becomes more pronounced when an excessive amount of DTBPS is injected during sulfiding operations conducted at temperatures below 500°F. To mitigate potential issues, the injection point should be positioned as close as possible to the catalyst bed, minimizing the risk of deposits in the preheating section that could accumulate on the piping and catalyst.
Gas phase sulfiding is not feasible to prevent solid formation. Additionally, DTBPS breaks down into Tertiary Butyl Mercaptan, a chemical with a strong odor.
Please note that this information is crucial for ensuring optimal catalyst performance and safety during the sulfiding process.
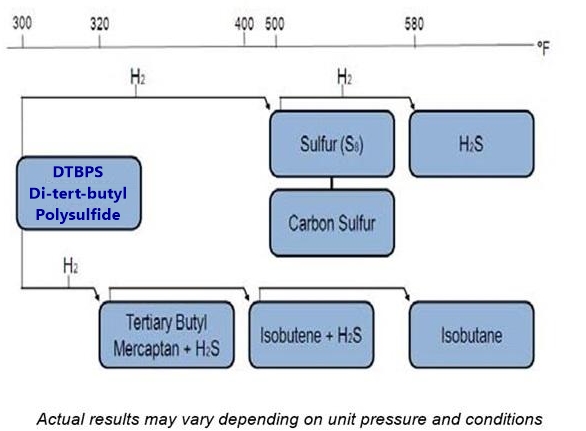
di-tert-butyl Polysulfide, DTBPS figures