For several years, expanded polystyrene (EPS) has been utilized as a material of choice in several food packaging applications, cost-effective and energy-efficient insulation in construction applications as well as cushion transport packaging material for shock sensitive goods and many more.
But, what is EPS? How is it manufactured? And, what are its key characteristics making it suitable in these applications?
Explore more about this polymer and find out its benefits, properties, recyclability etc. in detail.
Key features and benefits of EPS
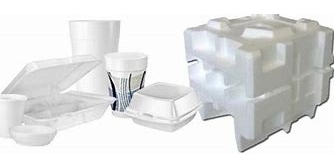
Expanded PolyStyrene (EPS) is a white foam plastic material produced from solid beads of polystyrene. It is primarily used for packaging, insulation etc. It is a closed cell, rigid foam material produced from:
- Styrene – which forms the cellular structure
- Pentane – which is used as a blowing agent
Both styrene and pentane are hydrocarbon compounds and obtained from petroleum and natural gas byproducts.
EPS is very lightweight with very low thermal conductivity, low moisture absorption and excellent cushioning properties. One of the serious limitations of polystyrene foam is its rather low maximum operating temperature ~80°C. Its physical properties do not change within its service temperature range (i.e. up to 167°F/75°C) for long term temperature exposure.
Its chemical resistance is nearly equivalent to the material upon which it is based – polystyrene.
EPS is 98% air and it is 100% recyclable
Some of the key producers of EPS include: BASF, NOVA Chemicals, SABIC, DowDupont, Synthos Group etc.
» View all EPS commercial grades and suppliers in Omnexus Plastics Database:
BASF (90)
Bewi Styrochem (23)
BorsodChem (Wanhua) (4)
Dioki (8)
DowDuPont (Dow) (1)
Go Yen Chemical Industrial Company (6)
Hyundai EP (16)
Idesa Petroquímica (9)
Ineos (16)
Iran Petrochemical (PCC) (10)
IRPC Public Company (16)
Jackon (21)
Kumho Petrochemical (14)
LG Chem (24)
Marco Polo International (5)
Monotez (Ravago) (11)
NOVA Chemicals (145)
PAK Petrochemical Industries (10)
Ravago Manufacturing Americas (8)
SABIC (16)
Samsung Cheil Industries (13)
Sekisui Plastics (29)
SH Energy & Chemical (21)
Sir Industriale (13)
Synbra Technology (8)
Synthos Group (67)
Taita Chemical (30)
Total Refining & Chemicals (4)
Versalis (Eni Group) (22)
This plastic database is available to all, free of charge. You can filter down your options by property (mechanical, electrical…), applications, conversion mode and many more dimensions.
How EPS is manufactured?
The conversion of expandable polystyrene to expanded polystyrene is carried out in three stages: Pre-expansion, Maturing/Stabilization and Molding
Polystyrene is produced from the crude oil refinery product styrene. For manufacturing expanded polystyrene, the polystyrene beads are impregnated with the foaming agent pentane. Polystyrene granulate is prefoamed at temperatures above 90°C.
This temperature causes the foaming agent to evaporate and hence inflating the thermoplastic base material to 20-50 times its original size.
After this, the beads are stored for 6-12 hrs allowing them to reach equilibrium. Then beads are conveyed to the mold to produce forms suited as per application.
Manufacturing Of Expanded Polystyrene Sheets/MoldsDuring final stage, the stabilized beads are molded in either large blocks (Block Molding Process) or designed in custom shapes (Shape Molding Process).
The material can be modified by the addition of additives such as flame retardant to further enhance fire behavior of EPS.
Expanded Polystyrene Properties and Key Benefits
EPS is a lightweight material with good insulation characteristics offering benefits such as:
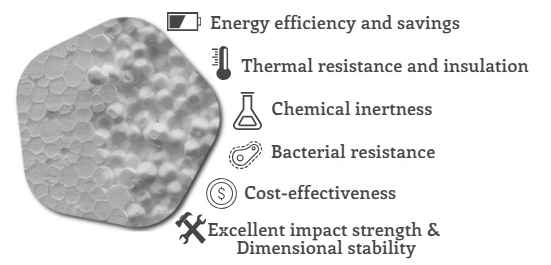
- Thermal Properties (insulation) – EPS has very low thermal conductivity due to its closed cell structure consisting of 98% air. This air trapped within the cells is a very poor heat conductor and hence provide the foam with its excellent thermal insulation properties. The thermal conductivity of expanded polystyrene foam of density 20 kg/m3 is 0.035 – 0.037 W/ (m·K) at 10 °C.
ASTM C578 Standard Specification for Rigid Cellular Polystyrene Thermal Insulation addresses the physical properties and performance characteristics of EPS foam as it relates to thermal insulation in construction applications. - Mechanical strength – Flexible production makes EPS versatile in strength which can be adjusted to suit the specific application. EPS with high compressive strength is used for heavy load bearing applications, whereas for void forming EPS with a lower compressive strength can be used.
Generally, strength characteristics increase with density, however the cushioning characteristics of EPS foam packaging are affected by the geometry of the molded part and, to a lesser extent, by bead size and processing conditions, as well as density. - Dimensional Stability – EPS offers exceptional dimensional stability, remaining virtually unaffected within a wide range of ambient factors. The maximum dimensional change of EPS foam can be expected to be less than 2%, which puts EPS in accordance with ASTM Test Method D2126.
Density (pcf) | Stress @ 10% Compression (psi) | Flexural Strength (psi) | Tensile Strength (psi) | Shear Strength (psi) |
1.0 | 13 | 29 | 31 | 31 |
1.5 | 24 | 43 | 51 | 53 |
2.0 | 30 | 58 | 62 | 70 |
2.5 | 42 | 75 | 74 | 92 |
3.0 | 64 | 88 | 88 | 118 |
3.3 | 67 | 105 | 98 | 140 |
4.0 | 80 | 125 | 108 | 175 |
Typical Properties of EPS Molding Packaging (70°F Test Temperature)(Souce: EPS Industry Alliance)
- Electrical Properties – The dielectric strength of EPS is approximately 2KV/mm. Its dielectric constant measured in the frequency range of 100-400 MHZ and at gross densities from 20-40 kg/m3 lies between 1.02-1.04. Molded EPS can be treated with antistatic agents to comply with electronic industry and military packaging specifications.
- Water Absorption – EPS is not hygroscopic. Even when immersed in water it absorbs only a small amount of water. As the cell walls are waterproof, water can only penetrate the foam through the tiny channels between the fused beads.
- Chemical Resistance – Water and aqueous solutions of salts and alkalis do not affect expanded polystyrene. However, EPS is readily attacked by organic solvents.
- Weathering and Aging Resistance – EPS is resistant to aging. However, exposure to direct sunshine (ultraviolet radiation) leads to a yellowing of the surface which is accompanied by a slight embrittlement of the upper layer. Yellowing has no significance for the mechanical strength of insulation, because of the low depth of penetration.
- Fire Resistance – EPS is flammable. Modification with flame retardants significantly minimize the ignitability of the foam and the spread of flames.
Extruded Polystyrene Vs Expanded Polystyrene
XPS is often confused with EPS. EPS (expanded) and XPS (extruded) are both closed-cell rigid insulation made from the same base polystyrene resins. However, difference lies in their manufacturing process.
Expanded Polystyrene (EPS) | Extruded Polystyrene (XPS) |
EPS is manufactured by expanding spherical beads in a mold, using heat and pressure to fuse the beads together. While each individual bead is a closed cell environment, there are significant open spaces between each beadEPS beads are molded in large blocks that are subsequently cut by hot-wire machines into sheets or any special shape or form by computer-driven systemsEPS’s blowing agent leaves the beads rather quickly creating thousands of tiny cells full of airEPS absorbs more water than XPS resulting in reduced performance and lost insulation power (R-value) | XPS is manufactured in a continuous extrusion process that produces a homogeneous “closed cell” matrix with each cell fully enclosed by polystyrene walls XPS is “extruded” into sheets. Polystyrene is mixed with additives and a blowing agent – which is then melted together through a dyeXPS’s blowing agent stays embedded in the material for yearsXPS is often selected over EPS for wetter environments that require a higher water vapour diffusion resistance valueThe compressive strength of XPS is greater than that of EPS |
Applications of Expanded PolyStyrene
Expanded polystyrene (EPS) is used for the production of a number of applications such as:
Building and Construction
EPS is widely used in building and construction industry thanks to its insulation properties, chemical inertness, bacterial & pest resistance, etc. Its closed cell structure allows only little water absorption. It is durable, strong and can be used as insulated panel systems for facades, walls, roofs and floors in buildings, as flotation material in the construction of marinas and pontoons and as a lightweight fill in road and railway construction.
Expanded polystyrene insulation offers numerous environmental advantages, including:
- Reduced energy consumption
- Recycled content
- Localized distribution and
- Improved indoor air quality

Food Packaging
EPS can be extruded using conventional equipment to form continuous sheet. This sheet may later be formed (e.g. using vacuum forming, pressure forming) to produce articles such as fruit trays, etc.
EPS does not have any nutritional value and hence it does not support fungal, bacteriological or any other microorganism growth. Therefore, it is widely used in the packaging of foodstuff such as seafood, fruit, and vegetables. The thermal insulating properties of EPS helps keep food fresh and prevent condensation throughout the distribution chain.

It is widely used material to produce food service containers like drink cups, food trays and clamshell containers.
When packed in EPS, fruits and vegetables retain their vitamin C content longer than food packaging in other materials.
Industrial Packaging
EPS packaging is often used for industrial packaging. It provides industrial products with the ideal material for complete protection and safety from risk in transport and handling thanks to its shock absorption property. This rigid lightweight foam can be molded into any shape for protecting and insulating sensitive products such as delicate medical equipment, electronic components, electrical consumer goods, toys as well as horticulture products during transport and storage.
EPS is also used to make disposable foam coolers and packing peanuts for shipping.
In packaging applications, Packaging density must be considered when
choosing the correct level of cushioning needed for the job
Other Applications of Molded EPS
EPS can be molded into any shape, examples:
- Sports helmets
- Infant car seats
- Chairs
- Seating in sports cars
- Load-bearing structurally insulated Panels etc.
EPS – Safety, Sustainability and Recyclability
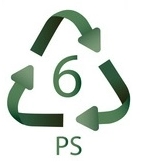
EPS Insulation is composed of organic elements – carbon, hydrogen and oxygen – and does not contain chlorofluorocarbons (CFCs) or hydrochlorofluorocarbons (HCFCs). EPS is recyclable at many stages of its life cycle.
Expanded Polystyrene is 100% recyclable and is designated by plastic resin identification code 6.
However, the collection of EPS can be a major challenge as the product is very light. PS recyclers have created a collection system in which the EPS is shipped over short distances to a facility where material is further processed by:
- Granulation – EPS is added into a granulator that chops the material into smaller pieces.
- Blending – the material is passed into a blender for thorough mixing with similar granules.
- Extrusion – the material is fed into the extruder, where it is melted. Color can be added, and the extruded material is then molded into a new value added product.
EPS materials can be reprocessed and molded into new packaging products or durable goods
Several countries have established formal expanded polystyrene
recycling programs throughout the world
Sustainability benefits associated with EPS are:
- EPS manufacturing does not involve the use of ozone-layer-depleting CFCs and HCFCs
- No residual solid waste is generated during its manufacturing
- It aids energy savings as it is an effecting thermal insulation material which helps reduced CO2 emissions
- EPS is recyclable at many stages of its life cycle
- EPS is inert and non-toxic. It does not leach any substances into the ground water
n-Pentane, CAS:109-66-0, in 130kg drums and Isotank,160 drums/40″GP, 80 drums/20″ GP, 15MT/Isotank
pentane #normal_pentane #normalpentane #CAS 109-66-0 #pentaneblends #pentanes #C5H12 #nPentane Please contact us to request a quote
Pentane Blends, CAS:109-66-0, in Isotank,15MT/Isotank
pentaneblend #pentaneblends #mixture_of_Isopentane_and Normal_Pentane #CAS109660