Basic knowledge of expandable polystyrene (EPS) Expandable polystyrene (EPS) is produced in a suspension process by adding a blowing agent, usually pentane, which causes resin to foam during moulding. The process may be performed as a single step or a two step process. The two step process passes the blowing agent though the polystyrene beads during, or after, polymerisation. Expanded polystyrene (EPS) is produced from a mixture of about 90-95% polystyrene and 5-10% gaseous blowing agent, most commonly pentane. The solid plastic is expanded using steam and is injected in to an aluminum tool under high pressure. Whether white or coloured, EPS starts life the size of a grain of salt. Polystyrene is produced from the crude oil refinery product styrene. For manufacturing expanded polystyrene, the polystyrene beads are impregnated with the foaming agent pentane. Polystyrene granulate is prefoamed at temperatures above 90°C.
Expanded polystyrene (EPS) is a light polymer made of the following materials:
- Styrene – forming honeycomb structure
- Pentane – used as blowing agent
Styrene and pentane are both hydrocarbons obtained from oil and natural gas by-products. EPS is composed of 98% air. Styrene, together with pentane, water and other chemicals, is converted into tiny EPS (expandable polystyrene) beads through a mixing reactor. The beads are then dried, sieved and finally coated.
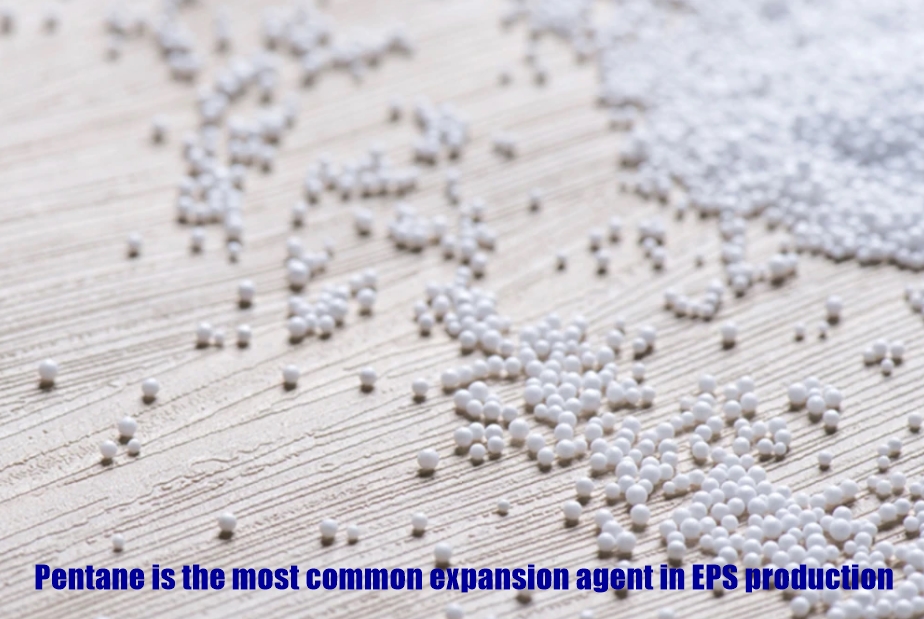
In 1950, BASF developed EPS, which was widely used in the construction field because of its excellent thermal insulation performance. Later, it was widely used in packaging because of its strong impact resistance.
EPS raw material beads have been mixed with blowing agent when they are produced, generally 4-7% pentane. High temperature steam foaming molding is used in the mold, and up to 98% of the finished products are air. The beads can be divided into flame retardant and non flame retardant, and can also be divided into large, medium and small according to the radius.
- Production process: pre foaming → curing → molding
- Pre foaming: use 80-100 ℃ steam to heat the raw material to increase the bead size by 40-50 times.
- Ripening: the prepared beads are dried in the silo to balance the internal pressure. The beads will have greater mechanical elasticity.
- Molding: the pre sent and dried beads are transferred to the mold, and the steam is added again to make the beads stick together to generate the finished product.
- Characteristics: low thermal conductivity, low density, high mechanical property, low water absorption, easy operation and installation, aging resistance, sound insulation and buoyancy.
The closed cell structure can cushion the impact by changing and restoring the deformation. The thermal conductivity is 0.033-0.043w / (m · K). Long term exposure to ultraviolet light will affect performance. It has no nutritional value, will not be eroded by mold, and will not decompose any water-soluble substance that pollutes groundwater.
A study by the packaging School of Michigan State University found that when fruits and vegetables are packaged with EPS, the carbon dioxide released by them will be retained, delaying maturation, and the content of vitamin C can be more effectively maintained.
Challenges facing the industry:
- 1. Fire. Flame retardant is usually added to improve the flame retardancy of EPS.
- 2. Recycling. Physical recovery method: the recovered compacted volume becomes 1 / 40 of the original, which is convenient for transportation and re production. The cost of the dissolution method is high. Used for incineration and energy recovery. EPS is not easy to degrade and can be used for landfill.